Several innovations and materials have contributed to enhancing the reliability and longevity of rod ends:
Advanced Materials:
- High-Strength Alloys: Use of advanced alloys, such as chromoly steel or stainless steel, offering improved strength and durability over traditional materials.
Coatings and Treatments:
- Corrosion-Resistant Coatings: Application of specialized coatings like zinc plating or chrome plating to protect against corrosion and extend the lifespan of rod ends.
Self-Lubricating Components:
- Maintenance-Free Materials: Integration of self-lubricating liners or materials (such as PTFE) within rod ends, reducing friction and wear, thus extending their lifespan.
Heat Treatment:
- Thermal Processing: Heat treatment techniques like quenching and tempering to enhance the hardness and toughness of materials, improving resistance to wear and fatigue.
Precision Manufacturing:
- Tighter Tolerances: Advanced manufacturing processes like CNC machining, allowing for tighter tolerances and more precise construction, enhancing overall reliability.
Sealed Designs:
- Enhanced Sealing Mechanisms: Improved seals or boots that protect against contaminants and retain lubrication, prolonging the lifespan of rod ends.
Composite Materials:
- Innovative Composites: Exploration of composite materials that offer a balance between strength, weight, and durability, contributing to longevity.
Reinforced Structures:
- Reinforcement Techniques: Incorporation of reinforced or strengthened sections within rod ends to handle higher loads and resist wear.
Innovative Design Features:
- Optimized Geometries: Enhanced design elements that distribute loads more evenly, reducing stress concentrations and increasing overall reliability.
Testing and Simulation:
- Performance Testing: Utilization of advanced testing methodologies and simulations to assess performance under various conditions, ensuring durability.
Customization and Tailoring:
- Application-Specific Solutions: Tailoring rod ends for specific applications or industries, optimizing their design and materials for enhanced reliability.
These advancements collectively contribute to improving the reliability, durability, and overall lifespan of rod ends in various applications, including automotive, aerospace, machinery, and industrial equipment.
What advantages do sealed or maintenance-free rod end offer compared to traditional designs?
Sealed or maintenance-free rod ends offer several advantages compared to traditional designs:
Reduced Maintenance:
- Elimination of Lubrication Needs: Sealed or maintenance-free rod ends incorporate self-lubricating materials or seals, reducing or eliminating the need for regular greasing or maintenance.
Longer Service Life:
- Extended Lifespan: By retaining lubrication and preventing contaminants from entering, sealed rod ends tend to have a longer service life compared to traditional designs, reducing replacement frequency.
Corrosion Resistance:
- Protection Against Contaminants: Sealed designs prevent dirt, moisture, and debris from entering, rod end supplier protecting the internal components against corrosion, wear, and damage.
Convenience:
- Ease of Use: Maintenance-free rod ends simplify upkeep, making them more convenient to use and reducing the time and effort spent on lubrication or maintenance tasks.
Reliability in Harsh Conditions:
- Consistent Performance: Sealed rod ends maintain their performance and functionality in harsh environments, resisting degradation due to contaminants or exposure to extreme conditions.
Cost Efficiency:
- Reduced Maintenance Costs: Lower maintenance requirements and longer service life contribute to cost savings over time, reducing the total cost of ownership.
Environmental Considerations:
- Less Environmental Impact: Maintenance-free designs reduce the need for lubricants, minimizing the potential environmental impact of grease or lubricant disposal.
Improved Safety:
- Enhanced Reliability: Sealed rod ends offer increased reliability by reducing the risk of failure due to lack of lubrication or contamination, enhancing overall safety.
Versatility:
- Adaptability to Applications: Sealed rod ends are suitable for various applications and industries, offering versatility without compromising performance.
Enhanced Performance:
- Consistent Operation: Maintenance-free designs maintain consistent operation over longer periods, ensuring stable and reliable performance in diverse conditions.
Reduced Downtime:
- Increased Uptime: With fewer maintenance requirements and extended service intervals, equipment fitted with sealed rod ends experiences reduced downtime.
Overall, sealed or maintenance-free rod ends offer improved convenience, longevity, reliability, and cost-effectiveness compared to traditional designs, making them a preferred choice for many applications, especially where reduced maintenance and extended service life are crucial.
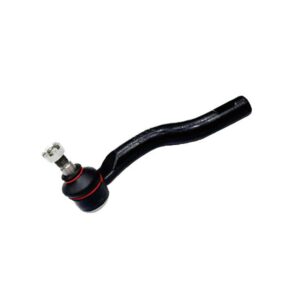