There are a few signs that can indicate worn out tie rod ends:
Excessive rattling or knocking noises when driving over bumps or steering the vehicle.
Worn tie rod ends loosen up and allow more side-to-side movement which results in the knocking sounds.
The steering wheel vibrating or pulsing when driving.
If the tie rod ends are worn out, the increased movement can transfer to the steering wheel.
Visible damage or excessive play in the tie rod ends.
Gently rock the tie rods up and down or side to side to check for movement beyond 1/4 inch. Worn ties rods will have significantly more play.
Loose or damaged end caps. The end caps hold together the internal tie rod threads and boot seal.
If a cap is damaged, broken or missing, it indicates the tie rod has been exposed to damage over time.
Corrosion on the tie rods or end caps.
Rust and corrosion speed up tie rod wear and damage. Heavy pitting is a sign tie rod ends have outlived their lifespan.
The steering wheel pulling to one side while driving or braking.
If the tie rods on one side are worn out, it causes the steering to become unbalanced which pulls the vehicle one way.
Visually inspecting the tie rods for signs of excessive grooving or threads that are damaged/stripped.
Extreme thread wear means the nuts can no longer provide a tight secure connection.
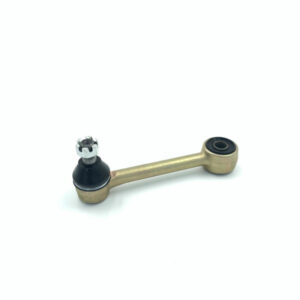
Having the vehicle alignment checked.
If pulling on the steering wheel, or uneven tread wear on tires is detected, it may indicate the tie rods have allowed the alignment to become out of specification. Tire rotation helps but won’t fix the underlying problem.
When in doubt, have the tie rod ends inspected by an alignment specialist or automotive repair technician.
They have the proper tools and experience to determine if tie rod end replacement is necessary for safe driving.
Making sure the tie rod ends have not outlived their useful service life is important for securing the steering and handling ability of the vehicle. If any problem symptoms are showing up, it’s best to get them checked by a tie rod supplier professional to avoid loss of control or damage.