Track rollers can be rebuilt or repaired under certain circumstances. Rebuilding or repairing track rollers can be a cost-effective alternative to outright replacement, especially if the rollers are still in decent condition and have not suffered extensive damage. However, it’s important to note that the feasibility of rebuilding or repairing track rollers depends on several factors, including the extent of wear or damage and the availability of suitable repair options.
Here are a few considerations:
Wear and Damage Assessment: Evaluate the condition of the track rollers to determine if they are suitable for rebuilding or repair. Minor wear, such as surface abrasion, can often be addressed through rebuilding or reconditioning processes. However, if the track rollers exhibit significant wear, cracks, or other structural damage, replacement may be the more appropriate option.
Rebuilding Processes: Rebuilding track rollers typically involves disassembling the rollers, cleaning them thoroughly, and replacing worn or damaged components such as bearings, seals, and bushings. Some specialized repair facilities or authorized dealers may offer services for rebuilding track rollers. The availability of rebuilding services may vary depending on the specific make and model of the track rollers.
Repair Options: In some cases, specific repairs can be performed on track rollers. For example, if there are minor cracks or localized damage, welding or other repair techniques may be employed to restore the functionality of the rollers. However, it’s important to consult with experts or authorized service providers to determine the suitability and safety of such repair methods.
Manufacturer Guidelines: Consult the manufacturer’s guidelines and recommendations regarding the repair or rebuilding of track rollers. Manufacturers often provide specific instructions and criteria for determining the repairability of their components. Following the manufacturer’s guidelines ensures that the repaired or rebuilt track rollers meet quality standards and maintain compatibility with the excavator.
Cost Considerations: Compare the cost of rebuilding or repairing track rollers to the cost of purchasing new ones. Rebuilding or repairing track rollers may be a cost-effective option if the necessary expertise and facilities are available. However, if the cost of rebuilding or repairing approaches or exceeds the cost of new track rollers, it may be more practical to opt for replacements.
Safety and Performance: Prioritize safety and performance considerations when deciding whether to rebuild or repair track rollers. It’s crucial to ensure that the rebuilt or repaired track rollers meet the required structural integrity, load-bearing capacity, and other performance specifications. If there are any doubts about the safety or effectiveness of the rebuilt or repaired track rollers, it is advisable to opt for new replacements.
When considering rebuilding or repairing track rollers, it is essential to consult with experts, authorized service providers, or the manufacturer to determine the most suitable course of action. They can assess the condition of the track rollers and provide guidance on the available repair options, ensuring that the repaired or rebuilt track rollers meet the necessary safety and performance standards.
What is the recommended procedure for adjusting track roller tension?
Adjusting track roller tension is an important maintenance task to ensure proper track alignment, undercarriage rollers performance, and longevity of the undercarriage system. The specific procedure for adjusting track roller tension may vary depending on the excavator model and manufacturer. However, here is a general recommended procedure:
Preparation: Park the excavator on a level surface and engage the parking brake. Shut off the engine and relieve any hydraulic pressure by moving the control levers back and forth. Ensure that all personnel are clear of the machine.
Inspection: Before adjusting track roller tension, inspect the undercarriage components, including track chains, sprockets, and track rollers, for any signs of wear, damage, or misalignment. Address any issues or abnormalities before proceeding with the adjustment.
Accessing Adjustment Points: Locate the adjustment points for track roller tension. These points are typically found on the track frame or the front idler assembly. Refer to the excavator’s user manual or manufacturer’s documentation for the specific location of the adjustment points.
Loosening Bolts: Loosen the bolts or nuts that secure the track roller frame or idler assembly. These bolts/nuts may be accessed from the side or bottom of the track frame. Use appropriate tools and follow the manufacturer’s instructions to loosen the bolts.
Adjusting Tension: Once the bolts/nuts are loosened, adjust the tension of the track rollers. This is typically done by moving the front idler assembly forward or backward, which affects the tension of the entire track assembly. Some excavators may have separate adjustment mechanisms for individual track rollers.
Proper Tensioning: Adjust the tension of the track rollers according to the manufacturer’s specifications. The appropriate tension may vary depending on the excavator model, operating conditions, and other factors. Follow the manufacturer’s guidelines or consult an authorized service provider for the recommended tension specifications.
Tightening Bolts: Once the desired tension is achieved, tighten the bolts or nuts that secure the track roller frame or idler assembly. Ensure that the bolts are tightened to the manufacturer’s recommended torque specifications. Over-tightening or under-tightening can affect the performance and lifespan of the track system.
Track Alignment Check: After adjusting the track roller tension, visually inspect the track alignment. The track should be properly aligned with the sprockets and other undercarriage components. Adjustments may be necessary if misalignment is observed.
Post-Adjustment Inspection: Conduct a final inspection of the undercarriage components, including the track rollers, to ensure proper tensioning and alignment. Look for any signs of abnormal wear, damage, or instability. Address any issues before resuming operation.
It’s important to note that the above procedure provides a general guideline, and it’s essential to refer to the specific instructions provided by the excavator manufacturer. Following the manufacturer’s recommendations and guidelines ensures that the track roller tension is adjusted correctly and in accordance with the equipment’s specifications.
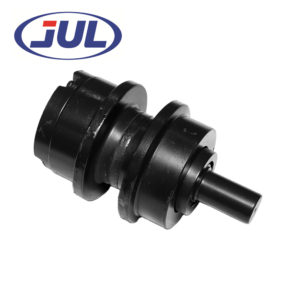